Merkmale von Fräsern
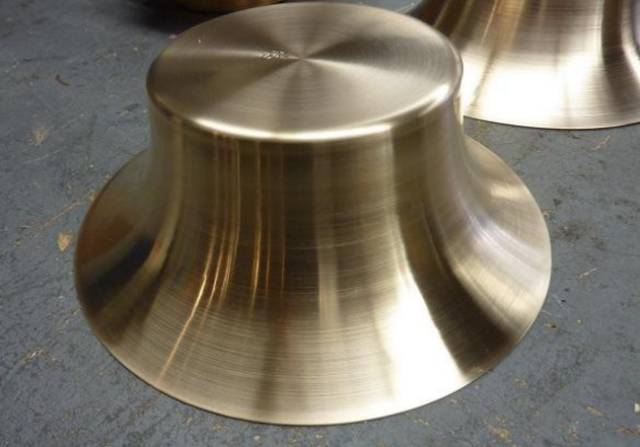
Der Versuch, die Steifigkeit der Vorrichtung vor Beginn der Verarbeitung zu erhöhen, wird der langfristigen Produktion in der Zukunft Vorteile bringen. Es verlängert nicht nur die Lebensdauer des Werkzeugs, sondern verbessert auch die Oberflächenqualität des Werkstücks und reduziert Bearbeitungsfehler.
Ebenso führt eine falsche Auswahl des Werkzeughalters zu einer Verkürzung der Werkzeuglebensdauer. Wenn beispielsweise ein Schaftfräser mit einem Durchmesser von 3,175 mm im Fräserhalter (anstelle des Federfutters) installiert ist, wird durch die Wirkung der Spannschraube der Passspalt zwischen Fräser und Fräserhalter auf eins vorgespannt Seite und die Mitte des Fräsers weicht ab. Der Drehpunkt des Werkzeughalters erhöht den Rundlauffehler des Fräsers während des Betriebs, was zu einer ungleichmäßigen Schnittbelastung an jedem Zahn des Fräsers führt. Insbesondere beim Fräsen von Nickelbasislegierungen ist dieser Schnittzustand nicht gut für das Werkzeug.
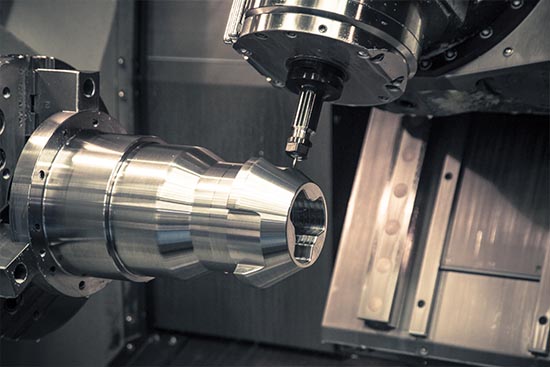
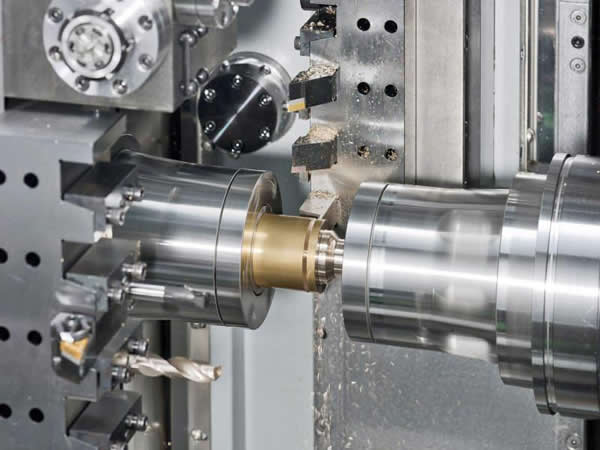
Durch die Verwendung eines Werkzeughalters, der die Exzentrizität der Werkzeugmontage verbessert, wie z. B. ein hydraulisches Spannfutter und ein Schrumpffutter, kann der Schnittvorgang ausgewogener und stabiler sein, der Werkzeugverschleiß wird reduziert und die Oberflächenqualität verbessert. Bei der Auswahl eines Griffs sollte ein Grundsatz beachtet werden, d. h. der Griff sollte so kurz wie möglich sein. Diese Anforderungen an die Werkzeug- und Werkstückspannung gelten für das Fräsen aller Materialien. Beim Fräsen von Nickelbasislegierungen sind nach Möglichkeit fortgeschrittene Bearbeitungserfahrungen erforderlich.
Verwendung von Werkzeugen
Unabhängig davon, wie das Werkzeug konstruiert ist oder aus welchem Material es besteht, sollte der Werkzeughersteller Ausgangswerte für Schnittgeschwindigkeit und Vorschub pro Zahn angeben. Sollten diese Daten nicht verfügbar sein, sollte die technische Abteilung des Herstellers konsultiert werden. Hersteller sollten wissen, wie gut ihre Produkte zum Nuten, Konturieren, Eintauchen oder Rampenfräsen über die gesamte Breite geeignet sind, da die meisten Standardfräser nicht für so viele Operationen geeignet sind. Verfügt der Fräser beispielsweise nicht über einen ausreichend großen zweiten Freiwinkel, verringert sich der Fasenwinkel beim Rampen.
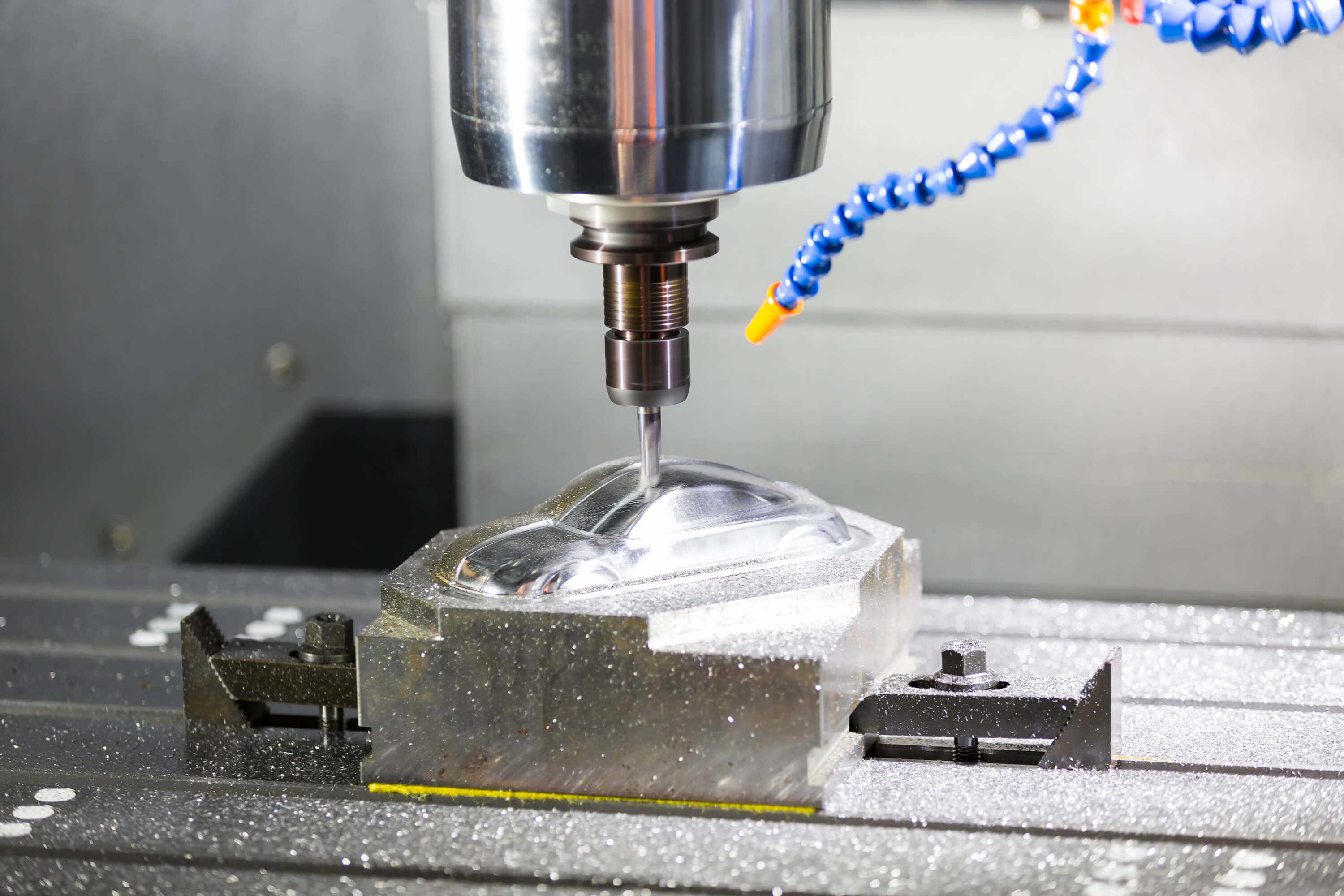
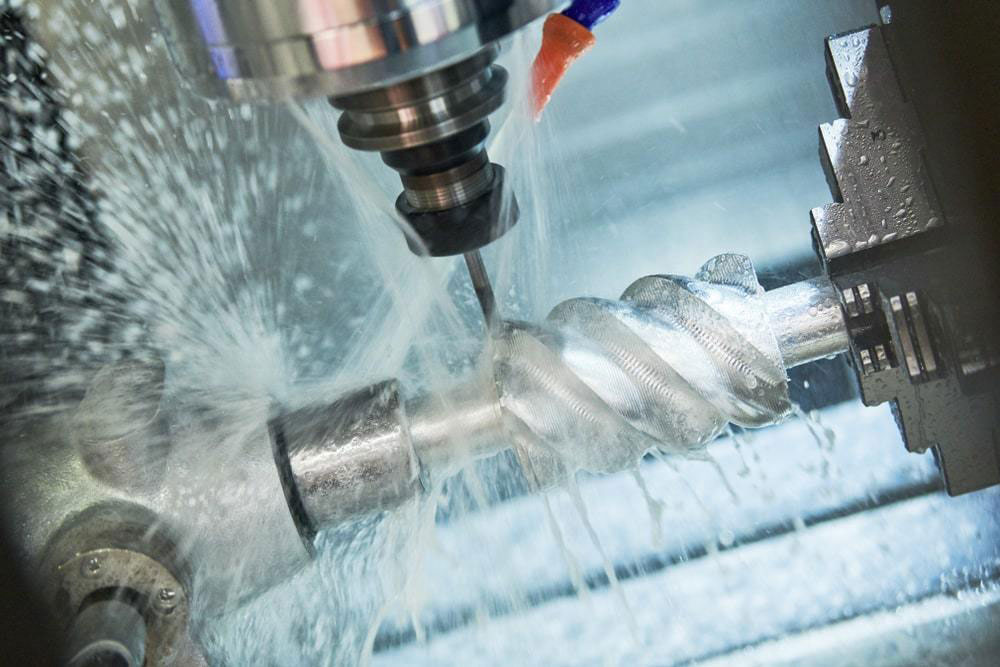
Wenn die Bearbeitungskapazität des Werkzeugs überschritten wird, führt dies natürlich zu Schäden am Werkzeug. Dasselbe gilt auch für das Tauchfräsen. Können die Späne nicht rechtzeitig aus dem Nutgrund ausgetrieben werden, werden die Späne gequetscht und das Werkzeug wird später beschädigt. Zusammenfassend lässt sich sagen, dass sich diese Bedingungen beim Fräsen von Superlegierungen negativ auf die Standzeit auswirken. Wenn Sie dachten, dass eine Verlangsamung der Vorschubgeschwindigkeit die Werkzeugstandzeit verlängern würde, dann haben Sie sich getäuscht. Ein typisches Beispiel ist, wenn beim ersten Schnitt festgestellt wird, dass das Material ziemlich hart ist. Wird der Vorschub reduziert (z. B. wird der Vorschub pro Zahn eines Wendeschneidplattenfräsers auf 0,025 bis 0,5 mm reduziert), reibt die Schneidkante des Werkzeugs stark am Werkstück, was zu einer Beschädigung des Werkzeugs führt schnell oder sofort. Durch Reibung kann es zu einer Kaltverfestigung der Werkstückoberfläche kommen. Um eine Kaltverfestigung zu vermeiden, sollte beim Schneiden des ersten Messers eine bestimmte Schnittlast (0,15–0,2 mm/Vorschub pro Zahn) eingehalten werden.
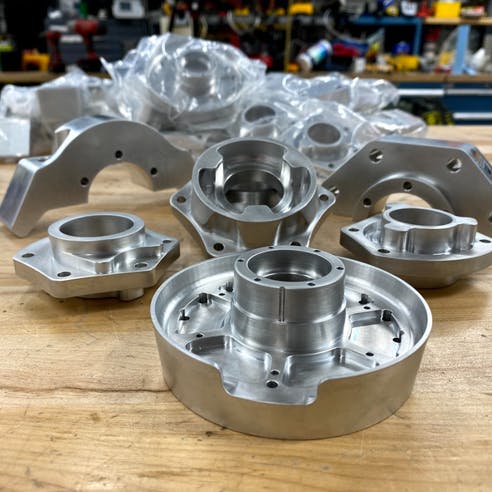
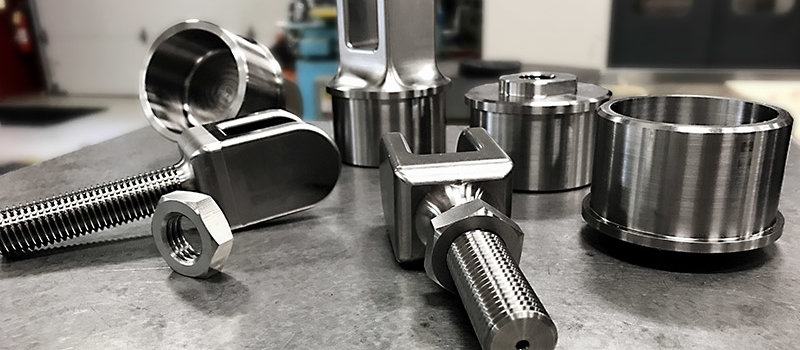
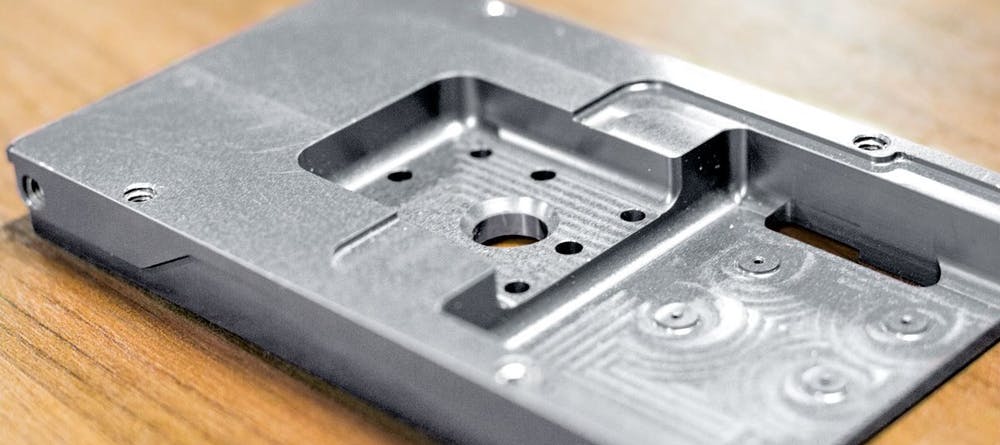
Senden Sie Ihre Nachricht an uns:
-
CNC-Bearbeitungsteile aus Aluminium
-
Herstellung von Aluminiumblechen
-
Hochpräzise CNC-Bearbeitungsteile von Axis
-
CNC-bearbeitete Teile für Italien
-
CNC-Bearbeitung von Aluminiumteilen
-
Bearbeitung von Autoteilen
-
Schmiedeteile aus Titanlegierung
-
Beschläge aus Titan und Titanlegierungen
-
Schmiedeteile aus Titan und Titanlegierungen
-
Drähte aus Titan und Titanlegierungen
-
Titanstäbe
-
Nahtlose Titanrohre/Röhren
-
Titangeschweißte Rohre/Röhren